機械部品賞
硬脆材加工用スクエアエンドミル DCMS
日進工具
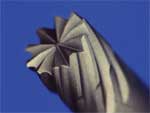
製品概要
日進工具の「硬脆材加工用スクエアエンドミル DCMS」は、硬くて脆い性質を持つ超硬合金やセラミックス、ガラスなどの材料を直彫り加工できる工具として開発した。工具の直径0.3m-2mmまでのサイズを量産化。微細で精密な金型や部品加工に対応する。
多刃形状を特徴とし、最小の直径0.3mmタイプでも6枚の刃数を持つ。1刃当たりの仕事量を減らして負荷を少なくし、硬脆材加工の課題である刃先の欠損を防いだ。超硬母材に密着力の高いダイヤモンド皮膜を施し、長時間安定して加工できるようにした。
硬脆材は、放電加工や砥石加工などの方法を使うのが一般的。ただ、金型や部品の小型・高精度化に伴い、コストと精度の両立が難しくなり、切削加工のニーズが強まっている。
DCMSを使えば、一般的な高速マシニングセンターによる加工が可能になる。特殊設備を追加導入する必要がなく、経済的な利点も大きい。微細・精密加工の領域は、海外へ流出せずに日本に残るとみており、DCMSの供給を通じて国内のモノづくりの高付加価値化に貢献する。
Voice
日進工具 代表取締役社長 後藤 勇 氏
昨年の「日本力(にっぽんぶんらんど)賞」に続き、今回「機械部品賞」を受賞させていただくことができ、当社を支えて下さっている多くの皆さまに心より感謝申し上げます。
国内製造業の空洞化が懸念される今、日本人らしい繊細で精密な微細加工という分野は、他国にはまねの出来ない匠の技であり、これに応える「日本に残すモノづくり」を行える工具をつくることが、小径工具に関して長年技術を培ってきた当社の使命であると常に感じながら研究開発を行っております。
「人と地球に優しい製品を開発し社会に貢献します」という当社の経営理念の実践に努力してまいりますので、今後ともよろしくお願い申し上げます。
エポックSUSシリーズ
日立ツール
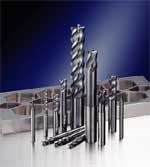
製品概要
日立ツールの「エポックSUSシリーズ」は、ステンレスを代表とする難削材を長時間、安定して切削できるエンドミルとして開発した。切削時の振動を抑制する不等分割刃型を採用。さらに、高剛性と切りくずの排出性を両立した2段ギャッシュ(底刃の溝)構造を採り入れた。これまで加工能率の向上が難しかった難削材の高速切削が可能になり、加工時間とコストを削減できる。傾斜切削などの難加工への対応、ドリル加工などの工程集約も実現した。
多種多様な部品加工用途に対応するため、スクエアタイプの「エポックSUSマルチ」と、外周刃を波形状にして切削抵抗を抑えたラフィングタイプの「エポックSUSウェーブ」の2種類を商品化した。前者は、長寿命な安定加工に向いている。一方後者は、工具断面形状を最適化し、クランプ状態の弱い複雑な加工物も安定して加工できるようにした。
一般的なエンドミルで切り込みの大きい荒加工を行う場合、2-3時間で工具寿命を迎える。これに対し「エポックSUSマルチ」は、18時間切削しても工具摩耗幅を0.1mm以下に抑えた。
Voice
日立ツール 代表取締役社長 田中 啓一 氏
今回開発した「エポックSUSシリーズ」は、主に部品加工分野をターゲットとして開発を進めてきた工具です。当社オリジナルの専用刃形を開発し、難削材であるステンレス鋼の加工において、能率・寿命ともに、従来よりも向上させることが可能となりました。更には、チタン合金、超耐熱合金等の加工においても性能を発揮します。
今回、機械部品賞を受賞できたことを光栄に思うとともに、今後もお客さまの抱えている問題を解決できる工具を開発すべく、モノづくりに励んでいく所存です。
E-LOCK四角溶接ナットタイプM4~M10
大阪フォーミング
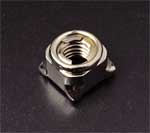
製品概要
大阪フォーミングの「E-LOCK四角溶接ナットタイプM4~M10」は、薄板などに溶接して使う緩み止めナット。ステンレス製で熱や経年劣化に強く、これまでボルト側の緩み止め加工やJIS規格を満たさないナットで対応するしかなかった場所で使える。約17分間のNAS式振動試験で脱落はなく、JISが定める強度区分「5」も実現した。
E-LOCKシリーズは、ナット上面に挿入した特殊リングがボルトのネジ山を押さえて緩み止め機能を発揮する。独自技術でリングのかしめ代を設けた台ナットを作り、ネジ高さを持たせて強度を確保した。同じ仕組みの他社製品はネジ山を削ってかしめ代を作るため、強度が下がっていたという。
特殊リングは、立体3枚バネの独自構造。強圧による塑性変形を防ぎ、長期に安定した戻り止め機能を発揮する一方、繰り返し使用を可能にした。
同製品は、既存設備で加工でき、工程も少なく、供給力、コスト競争力に優れる。同社は13年7月期にシリーズで売上高2億円を目指している。
Voice
大阪フォーミング 専務取締役 奥野 芳昭 氏
41年間、現在の本社で事業をさせていただき、下請け技術を育んできました。2年前にメーカーへの転身を決めて製作した製品が今回受賞できたことで、社員にも喜びの顔が伺えました。
会社は社員が一日の大半を過ごす場所です。仕事のやりがいは社員が一生をいかに楽しく過ごすかに関わります。
会社では一人の社員でも、みな家庭では大黒柱。会社が賞を取り、技術があると認められることは、それぞれが家庭で自慢できるモノを持つことになります。こういうモノを持てれば、次への意欲にもつながります。今後もこれにとどまらず精進し、よりよい製品を作っていきたいと存じます。
スティック IGS
フジキン
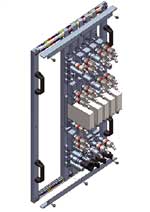
製品概要
フジキンの「スティックIGS(集積ガスシステム)」は、半導体製造装置のガス供給システム構築用に開発した。スティック1本で10種類のパターンを設定できる。6本のスティックの組み合わせにより、半導体製造装置用ガス供給システムの80%をカバーできる。通常、ガス供給システムは、1枚の板金上に約500点の部品で構築される。このためスティックIGSでは、ガスライン変更による改造や急な仕様変更にも柔軟に対応できる。
開発は、約1000種類のガス供給システムを分析し、バルブなどを配置する穴の位置を割り出しスティックに反映。そのつど設計していた個々の要素をパターン化、モジュール化し組み合わせて設計した。従来と同等以上の性能があり、設計生産効率は従来比2倍以上ある。
Voice
フジキン 代表執行役社長 兼 COO 野島 新也 氏
半導体製造においては、デザインルールの微細化が著しく進展し、微細化に伴いプロセスの高精度化と高生産性が要求されています。設備の稼働率を高め、製造コストを削減すべく、生産ラインのメンテナンス時間の最小化を図ることがお客さまのニーズです。
このたび当社が開発した「スティックIGS」は、これらに注力して設計製造を行ったものです。モジュール化、パターン化により、生産の標準化かつ海外生産も可能ならしめ、コスト削減効果が期待できます。この独創技術は、半導体業界並びに類似の各種の製造業における製造プロセスの信頼性と安定性の向上に貢献できるものと確信しております。
卓上プラズマエッチング装置
三友製作所
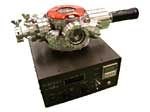
製品概要
半導体不良解析用に開発した「卓上プラズマエッチング装置」は、半導体素子を絶縁する酸化膜とプラズマ状態のガスを化学反応させることで、配線を露出させる。配線の状態を電子顕微鏡を通じて直接見られるため、不良状態をより簡便に特定できる。
化学反応を起こしながら気化させる独自技術の吸引プラズマを用いた局所的なエッチング装置のため、エッチング領域には常に新鮮なガスが供給され、反応生成物はすぐに排気される。プラズマを試料に噴出する従来型のプラズマエッチング装置に比べ、試料の残りかすや熱によるダメージを大幅に減少させた。また、従来、集束イオンビーム(FIB)で1日以上要していた配線の露出時間を100分の1以下の時間、10分の1以内の装置コストで実現し、装置の導入コストだけでなく、加工にかかる人件費を含めたコスト削減に寄与する。
同社は、過去にプラズマを試料に噴出するエッチング装置を試作。試料破壊や残りかすの問題にぶつかり、吸引で問題が解決することを発見した。
Voice
三友製作所 代表取締役社長 加藤木 克也 氏
半導体の不良解析用にプラズマを使ってエッチングする装置は他にもありますが、開発した装置は、局所的にエッチングし、配線を露出させた時に、配線を破壊せずにきれいに残したまま、絶縁膜を除去することができます。
配線の状態を電子顕微鏡を使えば確認できるため、熱で感知するセンサーを活用した装置に比べ、不良箇所が一目瞭然にわかります。今回、自社製品に初めて取り入れた「吸引プラズマ」は、画期的な手法だと考えています。また、プラズマエッチング装置はこれまで大きな装置が多く、卓上型は珍しいと聞いています。
こうしたことが評価されたのだと思っており、大変感謝しております。
デジタルゲージ DK800S
マグネスケール
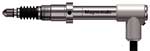
製品概要
機械部品の精度測定などに用いるデジタル式の長さゲージで、摺動回数を従来機種比6倍の3000万回に、定格荷重を同5倍の600ニュートンにそれぞれ高めた。スピンドルに設けた4条の溝と外筒の間にボールを組み込んだ、独自の「ボールスプラインベアリング構造」を採用。これにより耐久性の大幅な向上とともに、高精度で滑らか動作を実現した。
最高分解能は0.1μm(μは100万分の1)、精度は1μm。MR素子を使った磁気式の検出原理を採用しており、結露や油による精度への影響を受けにくい。ピストン機構部の工夫により、内部に水が入らないように配慮した。防水・防塵の規格である保護等級「IP67」にも対応する。
耐久性を高めたことで故障や摩耗などの不具合が少なくなり、メンテナンスの手間や費用を低減できる。自動車メーカーのパワートレインやドライブトレインの組み立て計測、光ディスクの組み立て計測などに採用。今後は、半導体デバイス生産設備や液晶生産設備への普及も見込む。
Voice
マグネスケール 代表取締役社長 藤森 徹 氏
当社のデジタルゲージは、自動車の製造ライン内での測定等に使用されることが多く、タクトタイムの短縮や長期信頼性、耐久性を求められる市場です。今までの製品も多くの顧客に採用いただいてまいりましたが、今回の製品は、ゲージの要ともいえる摺動機構部に新たな構造を取り入れることで、安定した精度での応答性、耐久性と信頼性を飛躍的に向上させることに成功しました。同時に保護等級性能の向上も得られるようになりました。この取り組みを評価いただき受賞に結びついたものと考えております。
今後も更なる技術の研鑽に努めて、日本のモノづくりの躍進に貢献していきたいと考えております。
ワイヤ放電加工機用高速ワイヤ電極 はやぶさ
ソディック/ソディックF.T
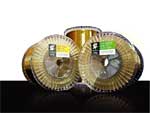
製品概要
面加工精度(面粗度)が低い上に価格が高く、普及が進んでいなかった高速ワイヤ電極のイメージを一新する製品として開発した。加工速度は一般的な真鍮ワイヤに比べて30%以上速く、面粗度は3μm(μは100万分の1)以下を実現した。従来の高速ワイヤの1kg当たり1500-2500円程度に対し、「はやぶさ」は同1200-1300円に低コスト化。真鍮ワイヤに200-300円の追加で販売可能にした。
ワイヤを自動的に放電加工機に装着する自動結線性能の成功率は、従来の高速ワイヤの50%前後に対し、「はやぶさ」は99%以上と飛躍的に向上した。銅と亜鉛を溶かす溶融工程から伸線工程に至る一貫生産体制を構築し、大幅なコスト削減を可能にした。
高速加工は、省エネルギー化につながり、ワイヤの消費量も平均で20%前後低減できる。同社は使用済みワイヤを回収し、新品同様の性能でリサイクルする独自の循環システムを運用している。「はやぶさ」もこれに対応し、省資源に貢献する。
Voice
ソディック 代表取締役社長 金子 雄二 氏
ワイヤ電極は、ワイヤ放電加工機に無くてはならない重要な部品であり、加工性能の向上に対して大きな影響があります。
今回、「ワイヤ放電加工機用高速ワイヤ電極 はやぶさ」の優れた高速性が評価され、このような栄誉ある賞をいただき、とても嬉しく思います。日頃の、”こんなものが欲しい”というお客さまからのご要望と、開発を担当した技術スタッフたちの”決してあきらめない”という気持ちと努力の成果であり、感謝の気持ちでいっぱいです。今後も、未来を創るソディックグループは、モノづくりに貢献できる技術革新に挑戦していきます。
パワーフィット
不二越
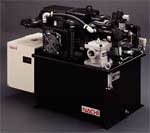
製品概要
不二越の「パワーフィット」は、標準的な製品と比べ消費電力を80%低減する省エネ型の油圧ユニット。油圧ポンプを電動機で駆動する油圧ユニットは負荷がない時も、ポンプを一定回転し続ける構造となっているが、本製品は可変容量ポンプとサーボモーターにより、負荷に応じて必要な分だけポンプを回転させるためエネルギーロスが少ない。必要な作動油量も少ないため、タンクを小型化でき、装置容積も大幅にコンパクト化した。
同社従来品の小型の省エネ型油圧ユニットに比べ、ユーザーの使い勝手も向上した。従来品は、指令ソフトや配線、制御盤などをユーザーが準備する必要があったが、本製品は単独でモーターの回転数やポンプの容量切り替えを制御するため、ユーザーはわずかな配線のみで運転可能だ。
最高圧力25MPa・最大流量毎分90の製品と、最高圧力28mPa・最大流量毎分140の2種類をラインアップ。
プレス機械向けの駆動源として販売が進んでおり、2011年の発売以来累計100台を出荷した。これまでは国内向け販売がメーンだったが、今後は海外でも展開する方針。
Voice
不二越 油圧事業部 技術部 久保 光生 氏
今回はこのような賞を頂き、誠にありがとうございます。本製品の省エネ性能が評価され、大変喜ばしく思います。
ポンプをサーボモーターで駆動する「パワーフィット」の開発には、産業用ロボット製造で蓄積したモーター制御技術を応用しましたが、それでもやはりモーターの回転数を制御しつつ、ポンプ容量を切り替えるアルゴリズムの設計が開発の難所でした。また、本製品は特にユーザーの使い勝手の向上を目指した製品であり、指令ソフトや制御盤が無くても使用出来るよう設計しています。
今後は、本製品で頂いたご意見・ご感想をもとに、海外対応品などを開発しラインアップを拡充する方針です。