自動車部品賞
低燃費タイヤ”SUPER ECO WALKER”
東洋ゴム工業
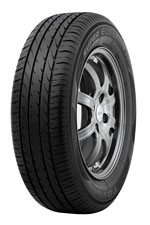
製品概要
東洋ゴム工業の「低燃費タイヤ”SUPERECO WALKER”」は、日本自動車タイヤ協会(JATMA )が定める低燃費タイヤのラベリング制度で、転がり抵抗性能「AAA(トリプルエー)」を初めて取得した商品。市街地走行時に同タイヤを装着した場合、燃費を2-3%向上できる。ウェットグリップ性能も一般的な市販用タイヤと同等に相当する「c」グレード。独自のゴム技術で相反する両性能を両立させて、低燃費で安全性の高いタイヤに仕上げた。
走行時に進行方向と逆の方向に作用する転がり抵抗を、同社従来の低燃費タイヤ比で約30%低減した。新開発のポリマー採用とシリカ配合量の最適化に加え、転動時に接地面の変形が少ないワイドなタイヤ形状にするなどで、タイヤ内部の発熱を抑制してエネルギー損失を低減。トレッドパターン(タイヤの溝)も、内部の発熱を抑えるリブパターンを採用した。
購入層は燃費意識の高い車ユーザーが中心。競合他社も低燃費タイヤに積極的で、市場は徐々に拡大してきている。
Voice
東洋ゴム工業 執行役員 タイヤ技術本部長 山本 卓司氏
多くのメーカーが環境配慮製品の開発に取り組んでいます。タイヤの環境性能における最高グレード「AAA(トリプルエー)」を初めて獲得した「”SUPER ECO WALKER”」は、乗用車用タイヤの潮流となりつつある低燃費志向の先駆け的な存在です。
「日本の部品産業が世界的な競争力の源泉である」との考えに立った顕彰制度は、モノづくりにいそしむ一製造業の立場からも非常に意義あるものと敬意を表しています。選出されたことに大変栄誉と誇りを感じるとともに、技術開発に携わる者への最大の励ましをいただいたものと受け止めています。
今後も価値あるモノづくりへさらなる情熱を注いでまいりたいと思います。
冷間成形ハブユニット軸受
日本精工
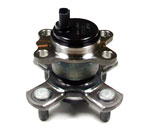
製品概要
ハブユニット軸受は、自動車の車輪を支える軸受とハブシャフトなど周辺部品と一体化した部品。燃費や乗り心地、操縦の安定性を向上させるため、軽量化が求められている。また、自動車メーカーの環境対応は急務となっており、軸受製造時まで含めたトータルの環境負荷低減の取り組みも必要になっている。
日本精工は、こうした需要にこたえるため、ハブシャフトの冷間成形で新工法を開発し、製造時の材料加熱エネルギーを従来より約70%低減、鋼材使用量を同20-30%削減した。また、冷間成形によって材料強度を高め、その向上分を軽量化設計に生かすことで同5%軽量化した。
フランジのような難加工材を冷間で成形する場合、材料を押しつぶすことで径を広げる加工方法では、成形の荷重が大きくなる課題がある。そこで同社は、金型内に素材を入れて端面を押すことで金型の側面にある穴から側方に押し出す「側方押し出し加工」を考案。これにより低い荷重でフランジ部を成形することが可能になった。
Voice
日本精工 執行役 技術開発本部 生産技術センター 所長
渡利 勝氏
ハブユニット軸受は、自動車の足回りに使用され、「走る」「曲がる」「止まる」を支える部品のため非常に高い信頼性はもちろん、燃費向上のため小型・軽量化も強く求められています。本ハブユニット軸受は、世界で初めて冷間成形での製造・量産化に成功し、従来の製品と同程度の強度を保ちながら、さらなる小型・軽量化を達成し、ダイハツ工業の新型「ムーヴ」の低燃費実現に貢献することができました。また、この製法は使用する鋼材使用量と電力量を大幅に削減でき、製造時も環境に貢献することができました。
当社は、今後も環境に優しく車の進化を支えるモノづくりを続けてまいります。
自動車部品用超軽量筐体「ECU BOX」
大成プラス(東京都中央区)
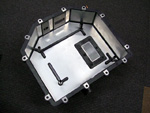
製品概要
肉厚が0.5mmのアルミ圧延材を有機系薬品に漬けて表面に直径10n–80nm(nは10億分の1)の凹凸を形成し、折り曲げ加工の後に射出成形機で樹脂を流し込んで接合して製造した筐体。樹脂とアルミニウムの接合強度は、25MPa–28MPa。金属を特殊処理してナノレベルの凹みを作り、樹脂と一体化する同社のNMT(ナノ・モールディング・テクノロジー)技術を生かした。
自動車のエンジンルーム内の基板を収めるため、車1台あたりこの筐体を50–60個使う。肉厚が2mm以上となるアルミダイカスト製と比べて60%以上軽量になるため、燃費向上や電気自動車(EV )の場合は走行距離向上が見込める。金型の寿命は8倍以上の80万ショットに延びる。切削加工やネジ穴加工が不要のため、製造コストを従来比で50%以上削減。発熱する部品上に銅製ヒートシンクを設置できるようにして放熱性を上げた。アルミと樹脂の接合部の気密性については、0.3MPaでの水素リーク試験に合格した。
Voice
大成プラス 代表取締役会長 成富 正徳氏
「薄肉成形ができない」「金型に掛かる負担が大きい」「後加工が必要」といったアルミダイカスト製品生産の短所をNMT技術で補いたい、と考えたのが開発のきっかけでした。現在「ECU BOX」の本格的な実用化に向けて、自動車メーカーとバックデータを集めています。自動車の軽量化への要求が高まっていることから、米国など海外からも引き合いが来ています。
金属と樹脂を接合する技術は他社にもあるが、NMT 技術は接着強度が高い点が特徴です。この技術を開発して約8年経つが、まだ知名度が高いとは言えません。受賞をきっかけにさまざまな人に広まっていけばうれしいです。