奨励賞
超硬油穴付きWDOドリルシリーズ
オーエスジー株式会社
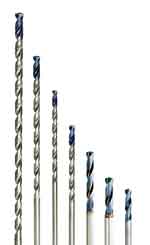
製品概要
「超硬油穴付きWDOドリルシリーズ」は、構造部品の組み立てに必要なネジ立ての前工程である下穴加工や、エンジン部品への穴あけなどに使われる。他社の従来工具に比べて約6倍の耐久性を持つために、工具再研磨の回数を高められ、結果的にランニングコストを90%以上低減できる。
新コーティング技術の採用で炭素鋼や鋳物の加工時のマージン損耗を大幅に抑えた。高速加工や高送り加工、工作機械の切削油を減らせる最小量潤滑(MQL)加工に対応したほか、消費電力を小さくするため低スラスト仕様とした。製品はロングタイプ339種、ショートタイプ306種の計645アイテムがある。
Voice
オーエスジー株式会社 代表取締役社長 石川 則男氏
栄えある「2011年”超”モノづくり部品大賞」奨励賞を受賞し、大変光栄に存じます。今回受賞した「超硬油穴付きWDOドリルシリーズ」は、自動車やトラック、産業機械などの製造現場の皆さまより「生産性の向上」「サイクルタイムの短縮」「耐久性の向上」といった数々の課題を頂戴し、皆さまの助言とご協力で生まれた製品です。この場をお借りして、ご協力いただきました関係の皆さまに心より感謝申し上げます。今後も常にお客さまの声をお聞きしながら、生産性の向上をはじめ、地球と人に優しいモノづくりに役立つ加工の提案、工具の開発を心がけてまいりたいと存じます。
ガストース
プラモール精工(宮城県富谷町)
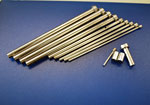
製品概要
「ガストース」は、プラスチック射出成形時に金型内部にたまるガスを効率的に抜く部品。バリ発生量を低減し、成形用樹脂の補充不足を解消する。エジェクターピンなどの代替として既存の金型に組み込んで使える。
補充不足による成形機の一時停止がなくなり、夜間の無人稼働などが安定する。原材料費や金型のメンテナンスコストを削減する効果もある。
ガストースの内部は空洞で、高温の樹脂から発生するガスを金型の外に排出する。金型内からガスを抜く穴の幅を0.05mm-0.005mmと細く設計することで、樹脂の流入を防ぐとともに、適度にガスが抜けるよう工夫した。
Voice
プラモール精工 代表取締役 脇山 高志氏
プラスチック射出成形が主力の当社にとって初めての自社製品が評価を受けたことをうれしく思います。
ガストースを開発したきっかけは、リーマン・ショックでした。受注の激減を効率化でカバーしようと試行錯誤した中でアイデアが生まれました。社内の成形機で使ってみると効果が非常に大きく、「困っている会社はほかにもあるはず」と考え、2010年4月に製品化しました。
また、自社製品を販売する中で顧客の声を聞き、新たな製品開発にも結びついています。東日本大震災で東北地域は大きな被害を受けましたが、事業を通じ、地域産業の復興に少しでも貢献していきたいと思っています。
光通信用グレーティング「近赤外S偏光高効率回折格子」
島津製作所
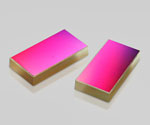
製品概要
島津製作所が開発した光通信や医療診断に適した回折格子「近赤外S偏光高効率回折格子」は、波長約800-n 1600n(mnは10億分の1)で相対回折効率90%前後と高精度の分光を特徴とする。近赤外領域で回折効率が高い、入射光が垂直方向のS偏光に特化して格子溝を形成することで実現した。
回折格子は、光を波長ごとに分ける光学素子。近赤外光は分析装置のほか、近年では光通信や医療診断に用いる波長モニターや波長可変レーザー、波長計測などにも用途が広がっている。高効率・高精度な近赤外光専用の回折格子により、新たな応用分野や新市場への普及も期待される。
Voice
島津製作所 常務取締役 安藤 修氏
当社の回折格子は、分析計測分野では国内トップシェアであり、性能や品質でお客さまのご評価をいただいてきました。
近年は、分析計測以外の新市場や欧米・アジアなどの海外へ積極的な展開を図っており、受賞製品は世界に通用する品質を目指して、新たに開発したモノづくり技術の成果です。
このたび、当社のデバイス製品が5期連続で表彰いただいたことを大変光栄に思うと同時に、この受賞は全て、お客さまからの多くのご支援の賜であると感謝しています。今回の受賞を励みに、世界の顧客に選ばれる社会に役立つ製品を提供できるよう、モノづくりに一層力を入れていく所存です。
大型リチウムイオン電池封止部品(ガスケット)
大和化成(堺市堺区)
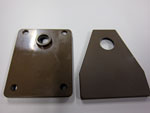
製品概要
リチウムイオン電池の電解液の漏れを防ぎ、同時に正極と負極を絶縁する部品。小型リチウムイオン電池用ガスケットで培ったノウハウをもとに大型用を開発した。素材には耐熱性、耐薬品性に優れたポリフェニレンサルファイド(PPS)樹脂を採用。製品のサイズがおよそ10倍になったにもかかわらず、寸法精度は小型と同じ20μm(μは100万分の1)以内を実現している。
さらに、自動車への搭載を前提に耐久性を向上し、品質保証期間を従来の7年から15年に延長した。現在は量産化に向け工程管理に注力しており、2011年度中に不良率0.000%1以下の達成を目指している。
Voice
大和化成 代表取締役社長 澤田 明伸氏
従業員20名あまりの当社が栄誉ある賞をいただけたことは社員の自信につながります。ありがとうございました。
当社は約30年前から二次電池用封止部品に特化した事業を展開しています。封止部品の一種であるガスケットは、電池の安全性を左右する重要な部品です。ただ、電極やセパレーターなどに比べ、注目を浴びる機会は多くありません。今回の受賞がガスケットの認知度向上に貢献することを期待しています。
電気自動車など向けの大型リチウムイオン電池は、ようやく普及期を迎えました。今後当社としては品質はもちろん、量産による低コスト化を進めることで電池の普及に貢献していく所存です。
GC研究用scaffoldシリーズ
ジーシー(東京都文京区)
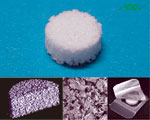
製品概要
ジーシーの「GC研究用scaffold(スキャフォールド)シリーズ」は、再生医療の研究用に特化したポリ乳酸系の細胞培養用基材だ。
3次元構造を持つため、厚みのある培養組織を作成できる。従来、ポリ乳酸系の基材は、スポンジ状で強度が弱い課題があった。同シリーズは成型方法を改良し、ある程度の硬さのブロック状にすることで、指で押してもつぶれない。
ブロックの表面には、100μm(μは100万分の1)前後の穴が開いており、細胞が自由に移動できる。栄養分も分散しやすく、細胞が育ちやすい。
Voice
ジーシー 代表取締役社長 中尾 眞氏
当社は、口腔内の健康を支える企業として創業90周年を迎え、健康長寿社会に貢献する世界一の歯科企業への挑戦をビジョンとして100周年を目指しております。
「GC研究用scaffoldシリーズ」は、今後発展が期待される再生医療の一助となるアイテムであり、歯科に限らず医療全般において国民のQOL(クオリティー・オブ・ライフ)の向上に貢献する医療技術の開発に寄与できるものであると考えております。
このたびの奨励賞受賞は、大きな励みであり、大変光栄に思っております。
高機能サニタリー用ソフトダイヤフラムバルブ
フジキン(大阪市北区)
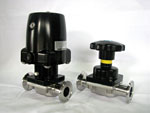
製品概要
フジキンの「高機能サニタリー用ソフトダイヤフラムバルブ」は、医薬・食品などの製造ライン用に開発した。従来品の課題であった外部漏れを防ぐシール性能を同社従来品比10倍以上に高めた。従来品のバルブ内部のダイヤフラムは、変性フッ素樹脂とゴムの二重構造。上下からゴムと共に締め付けていたため温度変化、経時変化で締め付け部がゆるみ、外部漏れにつながっていた。
新型は、ゴムを内側に閉じこめ、変性フッ素樹脂のみを締め付け、ゆるみを防止。液だまりも少なくなり洗浄性も高まる。屈曲性の高いフッ素
樹脂を用いて変形を抑え、同社従来品比で流量変化率は30分の1に低下した。
Voice
フジキン 代表取締役社長 野島 新也氏
医薬品、食品製造プロセスの対する品質要求は日々高まっており、常に正常な品質が維持できるよう多大の努力が払われております。これらの製造プロセスのより良好な操業には、キーツールとして重要な役割を担っているソフトダイヤフラムバルブの高い信頼性と安定性を確立する事は最重要事項とされております。
このたび、当社が開発した「高機能サニタリー用ソフトダイヤフラムバルブ」は、樹脂製とゴム製の2種類の膜の役割を明確にし、それぞれの膜の機能を効果的に発揮させることにより、これらのお客様の製造プロセスの信頼性と安定性の飛躍的な向上に貢献できるものと確信しております。
補助バッテリー搭載用ブラケット/ハイブリッド成形
小島プレス工業(愛知県豊田市)
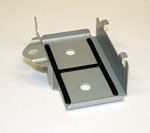
製品概要
インストルメントパネル内部に小型補助バッテリーを搭載するための金具。従来品は鉄板をプレス加工した本体に緩衝材となるフェルトを手作業ではり付けて生産していた。開発品はフェルトのはり付けを樹脂の射出成形に変更。プレス機と小型射出成形機を組み合わせたハイブリッド成形機を開発し、金属と樹脂の同時成形を可能とした。
プレス機も特徴的で、金型を上下に重ねた構造をしており、1台で複数のプレス加工ができる。ハイブリッド成形機は、素材投入から完成までを1台で完結する。中間在庫や設備費などの大幅な削減を実現した。開発品はトヨタ自動車の2車種に採用されている。
Voice
小島プレス工業 第2技術部 部付主担当員 竜嶽 正紀氏
このたびは奨励賞を受賞することができ、心から感謝申し上げます。 今回の開発は、原価低減活動を発端に、二次加工を一次加工に取り込むことを目標にした当社独自の「提灯プレス機」「小型射出成形機」という二つの技術を融合し、金属と樹脂の同時成形を実現しました。その結果、中間在庫ゼロ、組み付け作業者ゼロのコンパクトな「自工程完結ライン」を達成しました。これによりコスト低減、品質の安定化、さらに脱脂工程廃止による作業環境の改善、離型紙の全廃など環境にもやさしい製品となりました。 今後も、お客さまの製造現場に喜ばれるモノづくりを継続していきます。